USE-CASES
Aufbauend auf der „Sustainability Monitoring Platform“ gilt es, eine KI-basierte Engine zu entwickeln, welche unternehmensindividuelle ZERO³ Potenziale identifiziert. Auf Basis der so identifizierten ZERO³ Potenzialen sind Verbesserungs- und Umsetzungslösungen zu den drei verschiedenen Nachhaltigkeits-Trade-Offs (Ressourcen, Mensch und Daten) zu identifizieren und praxisgerechte Handlungsfelder sowie Umsetzungsmaßnahmen als priorisierte Entscheidungsgrundlage der österreichischen herstellenden Industrie transparent zu kommunizieren. Die KI-basierte Engine ist unter Berücksichtigung der beteiligten Industriepartner zu entwickeln und zu validieren. Die entsprechenden Verbesserungs-/ Umsetzungslösungen sowie damit verbundene praxisgerechte Handlungsfelder und Maßnahmen in den folgenden drei ZEROs zu analysieren, zu entwickeln und zu validieren. Die Abbildung ordnet die Usecases übergeordneten den identifizierten Nachhaltigkeitsdimensionen (Zero Ressource Loss, Zero Data Gap und Zero Human Potential Loss) zu.
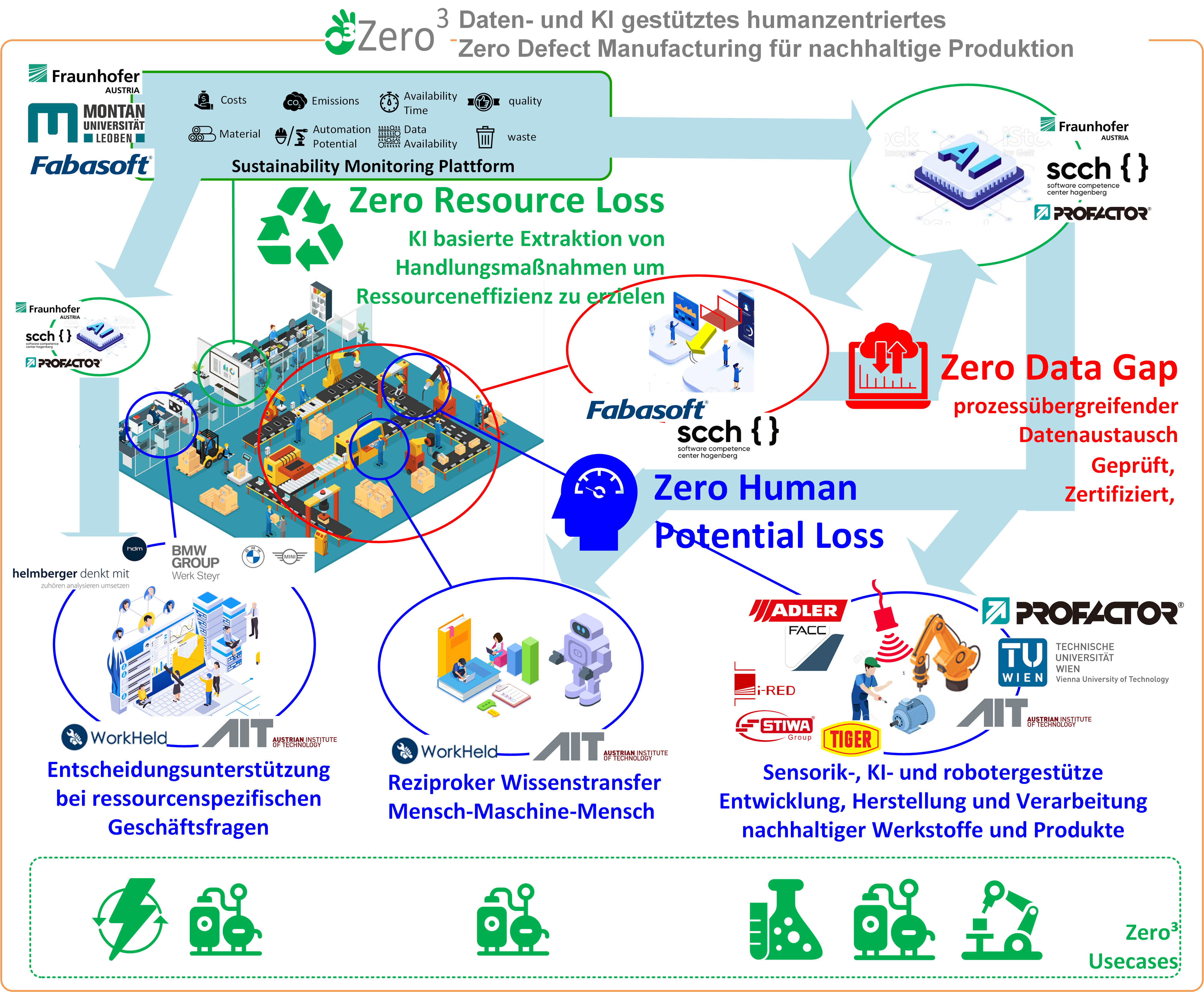
Das Projektkonzept von ZERO³ verdeutlicht eine datenbasierte Möglichkeit für Österreichs Industrie durch Einsatz der zu entwickelnden “Sustainability Monitoring Platform” zentrale Engpässe in unternehmensindividuellen Produktionsprozessen zu identifizieren und Lösungen in Form von Technologieentwicklungen im Rahmen von KI- und Robotiksystemen sowie in Form von anwendungsspezifischen Handlungsfeldern und Umsetzungsmaßnahmen aufzuzeigen und deren Umsetzung im Sinne ökologischer, ökonomischer und sozialer Verbesserungen zu verdeutlichen.
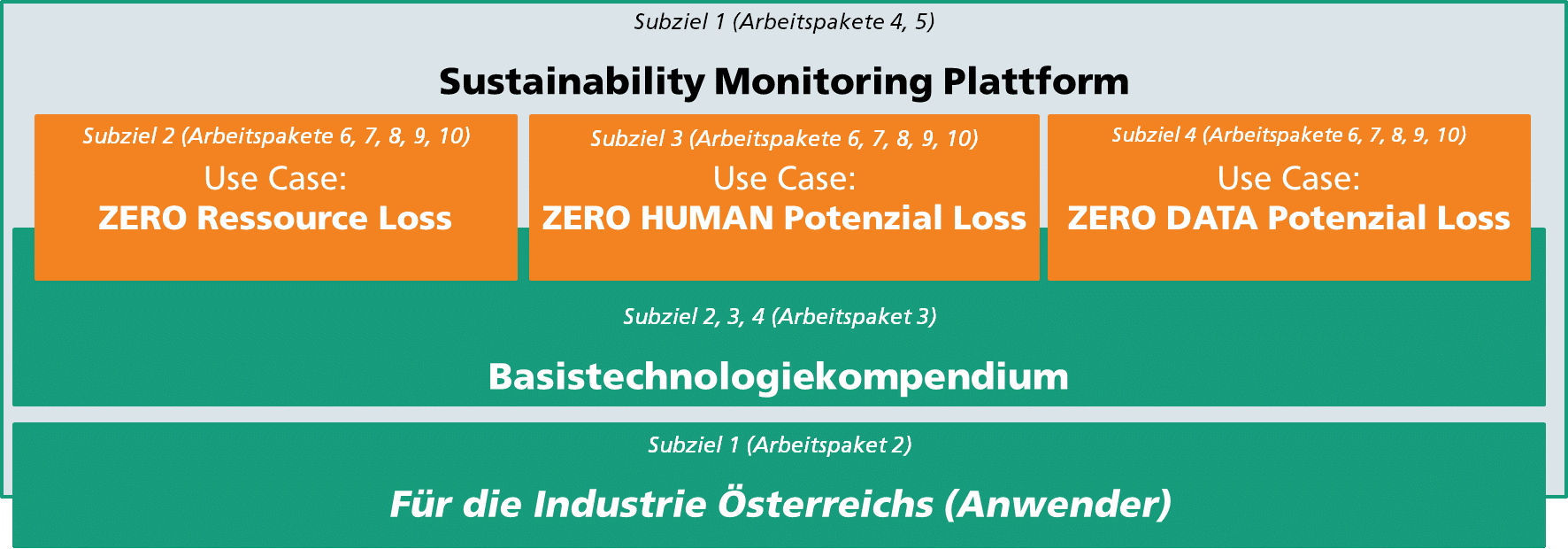
Use-Case: Resourceneffizienz durch KI-optimierte Energie- und Medienströme
Facilitymanagement ist ein ganzheitlicher, strategischer und lebenszyklusbezogener Managementansatz, um Facilities, ihre Systeme, Prozesse und Inhalte kontinuierlich bereitzustellen, funktionsfähig zu halten und an die wechselnden organisatorischen und marktgerechten Bedürfnisse anzupassen. In der Sachgüterproduktion optimiert Facility Management so den Betrieb, die Wirtschaftlichkeit, die Nutzung aller Einrichtungen einschließlich aller hierfür notwendigen Prozesse und erreicht dadurch eine ganzheitliche und umfassende Infrastrukturerstellung, -bereitstellung und -bewirtschaftung mit dem Ziel, die Produktivität bzw. Ressourceneffizienz langfristig zu steigern. Aktuell können nur etwa 80% der Ressourcen- und Medienverbräuche nachvollzogen werden. Speziell in der flexiblen Variantenfertigung, oder bei kurzfristigen Produktionsausfällen bzw. –umschichtungen bleibt der Rest ungeklärt. Das macht es schwierig Anomalien und Verschwendung im Verbrauch zu identifizieren bzw. Abnahme-Prognosen wie sie von Energieversorgern eine Woche im Voraus abzustimmen.
Einsatzbereiche und Herausforderungen
Aktuell ist eine flächendeckende Erfassung, Zusammenführung und dezentrale Bereitstellung aller notwendigen Daten (ZERO Data Gap) für eine präzise Prognose oft nicht gewährleistet. Der Zusammenhang von Medienverbräuchen und einzelnen Produkten oder Produktvarianten ist unklar. Daher ist es schwierig Anomalien (Leckagen, deaktivierte Energiesparmodi) in der laufenden Produktion zu erkennen oder präzise Vorhersagen zu erstellen. Verschiebungen von Hochlaufphasen können helfen teure und ineffiziente Ressourcenverbrauchsspitzen (ZERO Resource Loss).
Zielsetzungen
- Identifikation von relevanten Teiloptimierungsmöglichkeiten im Facility-Management und Bewertung des Einsparungspotentials im Hinblick auf Ressourcen.
- Identifikation von aktuell vorhandenen Data- und Interoperabilitäts-Gaps die die Behebung von Ressourcen-Verlusten verhindern.
- Entwicklung und Einsatz einer “Sustainability Monitoring Platform” mit welcher KI-unterstützt Anomalien erkannt, Verbrauchsprognosen erstellt und ressourcenspezifische Geschäftsentscheidungen getroffen werden können.
Use-Case: Ressourceneffizienz durch Entwicklung von nachhaltigen Materialien und nachhaltigen Verarbeitungsprozessen
Materialwissenschaft und Werkstoffkunde beschäftigen sich mit der Herstellung von Materialien und deren Charakterisierung von Struktur und Eigenschaften bzw. Entwicklung von Werkstoffen sowie entsprechenden Verarbeitungsverfahren. Es ist zunehmend wichtig, die Entwicklung, Herstellung und Einsatz von nachhaltigen Werkstoffen zu beschleunigen bzw. die Effizienz bei der Verarbeitung zu steigern. Nachhaltige Lacke, Farben und Tinten haben in der Regel neben längerer Lebensdauer einen kleineren CO2-Fussabdruck und basieren auf nachhaltigen Rohstoffen. Es gilt zudem die Effizienz von Herstellungsverfahren zu steigern um eine möglichst effiziente Skalierung von der Herstellung auf Laborniveau hin zur Produktion für den Markt zu gewährleisten. Auch bei der Verarbeitung der Produkte kann die Effizienz durch die Vermeidung von Fehlern weiter gesteigert werden.
Zielsetzungen
- Entwicklung von Sensoren und KI-basierten Auswerteverfahren für die Charakterisierung der Veränderung der Oberflächenqualität von Lacken durch chemische Substanzen, und das reziproke Erlernen der Beurteilung durch KI-System und (anzulernende) Mitarbeiter.
- Entwicklung von Sensoren und KI-basierten Auswerteverfahren für die Charakterisierung von Prozess- und Materialdaten um automatisch Parameter für das upscaling von Herstellprozessen von Tinten und Pigmentpasten ableiten zu können.
- Entwicklung von thermografischer Bildaufnahmetechnik und KI-basierten Segmentierungsmethoden für die Defekterkennung bei der Herstellung von CFK-Bauteilen.
- Entwicklung von Datenschnittstellen zur “Sustainability Monitoring Platform” um stations- und standortübergreifende Interoperabilität und Zugänglichkeit der Daten ermöglicht werden kann.
- Entwicklung von Konzepten für effiziente Mensch-Roboter Kollaboration um einerseits optimale maschinelle Unterstützung und Entlastung bei unergonomischen Prozessen zu erzielen und nicht automatisierbare Prozesse (z.B. Entscheidungen, …) optimal zu unterstützen.
- Darstellung der Entwicklungsinhalte entlang der Materialwertschöpfungskette in 3 relevanten Teilusecases
Einsatzbereiche und Herausforderungen
Die effiziente Entwicklung von (nachhaltigen) Tinten und Lacken benötigt automatisierte und objektive Prüfverfahren. Aktuell ist die Prüfung der chemischen Beständigkeit von (nachhaltigen) Lacken und Werkstoffen nicht automatisiert. Es werden einerseits zahlreiche Lebensmittel und Haushaltschemikalien manuell appliziert, bedeckt und nach definiertem Zeitraum wieder abgewaschen. Andererseits werden Zustand und Art der Oberflächenbeeinträchtigung in diversen Kategorien manuell.
Beim Herstellungsprozess von Tinten werden sowohl Pigmentpasten hergestellt, als auch Lösungsmittel aufbereitet die anschließend gemischt und gefiltert werden. Dabei wird bei der serienmäßigen Herstellung gemäß Rezepturen vorgegangen, die bei der Tintenentwicklung für kleinere Maßstäbe erarbeitet wurde. Es besteht die Vermutung, dass einige Prozessschritte möglicherweise früher beendet werden.
Use-Case: Flexible Produktion zur Herstellung hochwertiger Produkte
In der Automobil-Zulieferindustrie bzw. der verfahrenstechnischen Industrie sind Herstellprozesse und zu produzierenden Mengen meist sehr gut vorhersehbar. Projektlaufzeiten erstrecken sich meist über mehrere Jahre wodurch die Produktion planbar wird und internationale Wertstromketten für die Herstellung von Einzelteilen und Montagebaugruppen bzw. notwendige Herstellprozesse und die begleitenden Prozesse wie bspw. Qualitätssicherung gut planbar werden.
In der Elektronikindustrie stellen kurze Entwicklungs- und Produktlebenszyklen, neue Materialien und komplexe physikalische Wirkprinzipien für mechatronische Produkte die Entwicklung und die Serienproduktion vor große Herausforderungen. Nachhaltigkeit und Effizienz müssen von Beginn an bestmöglich berücksichtigt werden um einerseits vom Serienhochlauf an möglichst schnell am Optimum zu produzieren und andererseits eine skalierbare Produktion zu ermöglichen. Um Produktionsaufträge der Elektronikindustrie zu erhalten, sind zunehmend Dokumentation und Nachweis des CO2 Fußabdrucks der Herstellung des Produkts erforderlich. Je innovativer und einzigartiger dabei die hergestellten Produkte (z.B. frei programmierbare magneto-rheologische haptische Bedienelemente) desto schwieriger diese Aufgabenstellung.
In der Automobil-Zulieferindustrie bzw. der verfahrenstechnischen Industrie sind Herstellprozesse und zu produzierenden Mengen meist sehr gut vorhersehbar. Projektlaufzeiten erstrecken sich meist über mehrere Jahre wodurch die Produktion planbar wird und internationale Wertstromketten für die Herstellung von Einzelteilen und Montagebaugruppen bzw. notwendige Herstellprozesse und die begleitenden Prozesse wie bspw. Qualitätssicherung gut planbar werden.
In der Elektronikindustrie stellen kurze Entwicklungs- und Produktlebenszyklen, neue Materialien und komplexe physikalische Wirkprinzipien für mechatronische Produkte die Entwicklung und die Serienproduktion vor große Herausforderungen. Nachhaltigkeit und Effizienz müssen von Beginn an bestmöglich berücksichtigt werden um einerseits vom Serienhochlauf an möglichst schnell am Optimum zu produzieren und andererseits eine skalierbare Produktion zu ermöglichen. Um Produktionsaufträge der Elektronikindustrie zu erhalten, sind zunehmend Dokumentation und Nachweis des CO2 Fußabdrucks der Herstellung des Produkts erforderlich. Je innovativer und einzigartiger dabei die hergestellten Produkte desto schwieriger diese Aufgabenstellung.
Zielsetzungen
- Entwicklung nachhaltiger, skalierbarer Produktionskonzepte von Produktion mit Mensch-Roboter-Kollaboration bis hin zur Vollautomatisierung zur flexiblen Produktion hochwertiger Produkte.
- Wertschöpfungsketten und Produktionsprozesse durch die “Sustainability Monitoring Platform” einfach auf deren Nachhaltigkeit bewertbar machen.
- Schaffung einer Möglichkeit mit Hilfe von Robotik und KI die Typenvarianz in der Produktionslinie zu beherrschen. Heutige Systeme sind hier typenspezifisch gebaut und programmiert und nur mit großem Aufwand auf neue Typen zu adaptieren. KI Methoden sollen diese Integrationszeiten auf ca. 1 Tag/Typ reduzieren.
- Schaffung einer Möglichkeit, das Wissen von Mitarbeitern und aus der Grundlagenentwicklung möglichst effizient auf die Produktionsanlage zu übertragen.
- Schließung von Data Gaps um Entwicklung und Etablierung einer Methode um in der Kaskade von Produktionsumgebungen die effizientesten Optimierungen einfließen zu lassen und Aufbauend auf die Visualisierung und Analyse dieser Daten die richtigen Geschäftsentscheidungen zu treffen.
- Schließung von Data Gaps zur Entwicklung und Etablierung einer Methode um in der Kaskade von Produktionsumgebungen die effizientesten Optimierungen einfließen zu lassen.